金型の設計から金型製作、試作品作成、プラスチック成形、量産、検査、品質管理まで一貫した生産体制を確立しています。
事前のお打ち合わせからスピーディーに製品をお届けいたします。
- 事前打ち合わせ
- お客様と打合せを行い、製品と金型の要望を満足できる金型の構造・型割り等の概要設計を決めます。
製品の詳細な仕様決定の打ち合わせを行います。できるだけ無駄なコストをかけないように、さまざまな要件の取り決めをこの段階で行います。
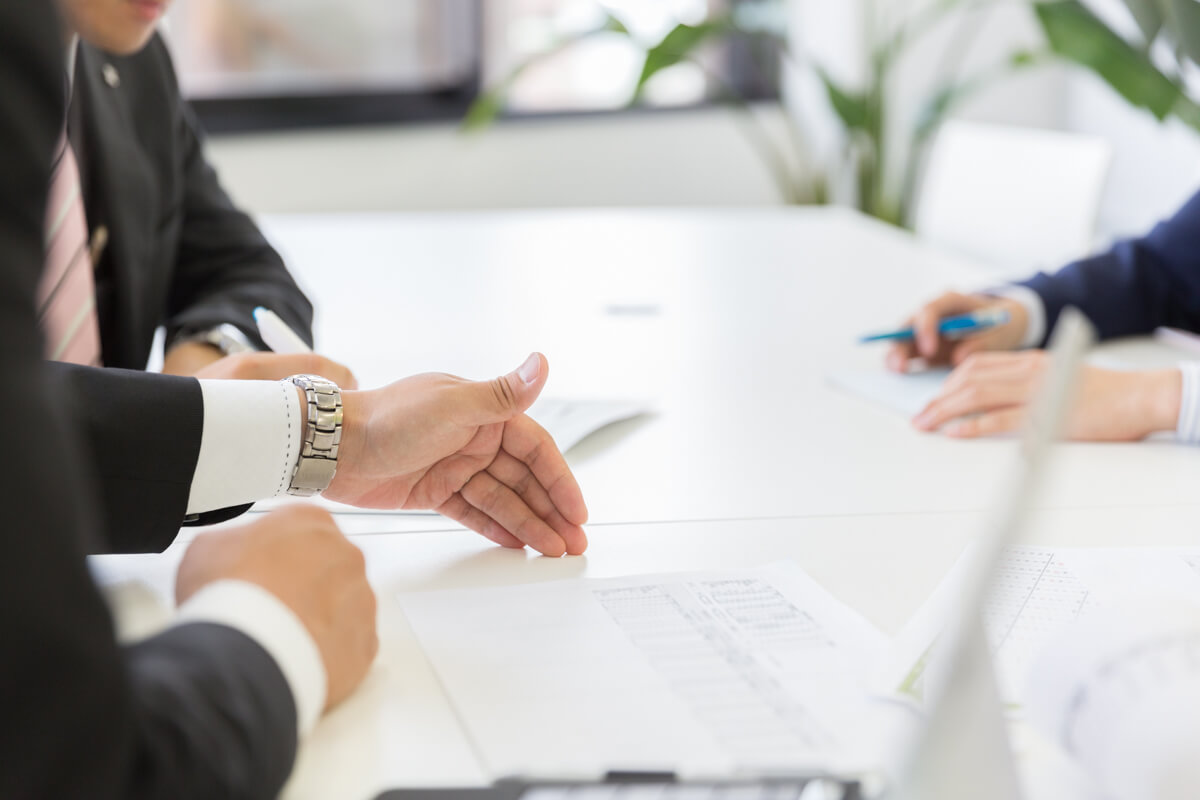
- 設計
- 金型の3D設計を行います。
お客様の仕様を基に成形性・耐久性・メンテナンス性・加工性を考慮して金型の設計を行います。
製品材料毎に成形後の変形量(収縮率)が異なる為、重要箇所に金型補正代(後から金型を削れる方向に大きく製作)を見込んで設計します。
試作後の測定データを基に金型削り量を決め、図面データを更新します。
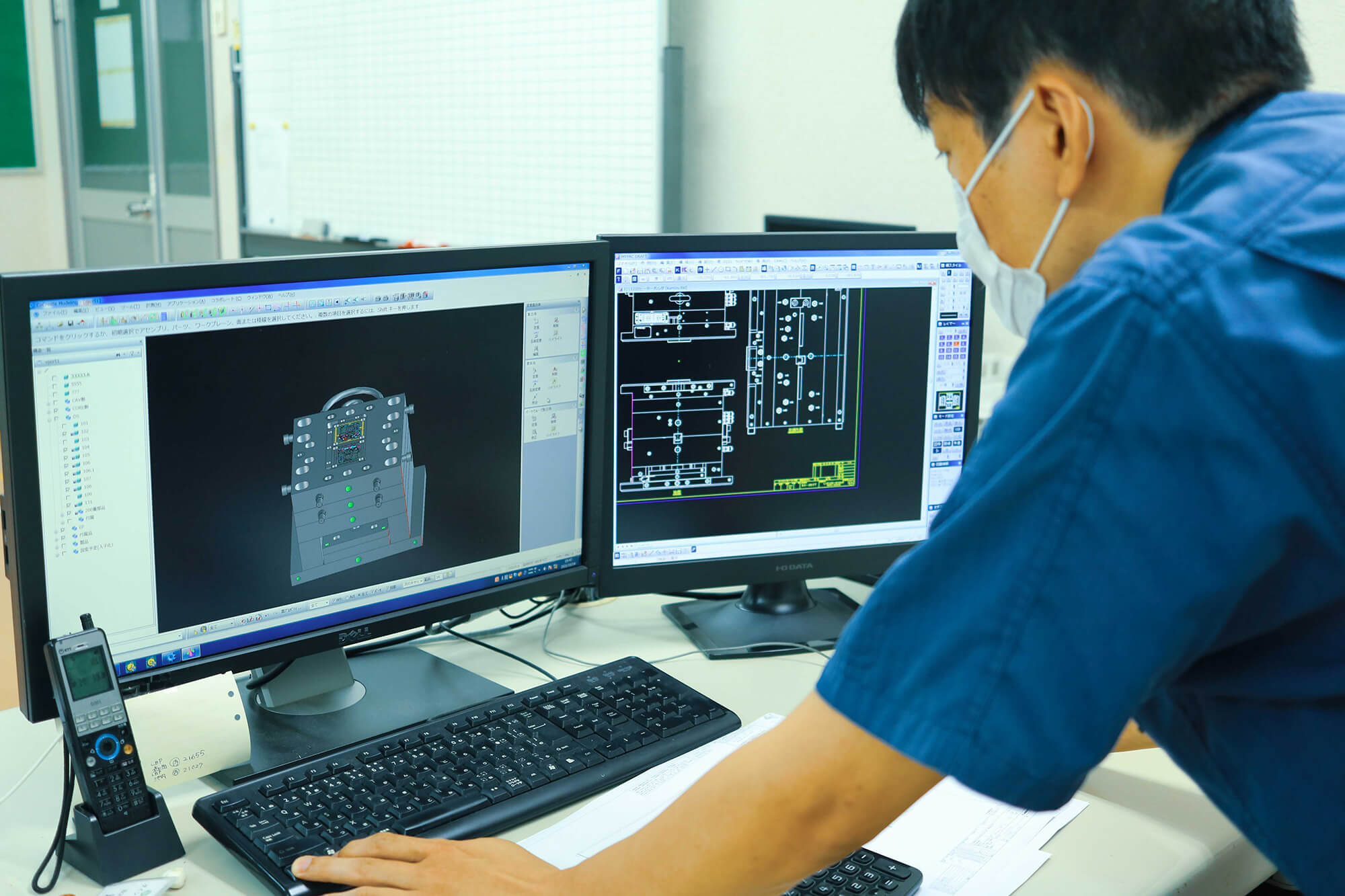
- 加工データ作成
- マシニング加工やワイヤー放電加工の加工プログラム(NCプログラム)の作成を行います。
金型の形状(モデル)を確認し、最適な加工工程を検討して使用工具・加工条件を決めるなど、各種加工機に精通したプログラム作成者のノウハウが必要となります。
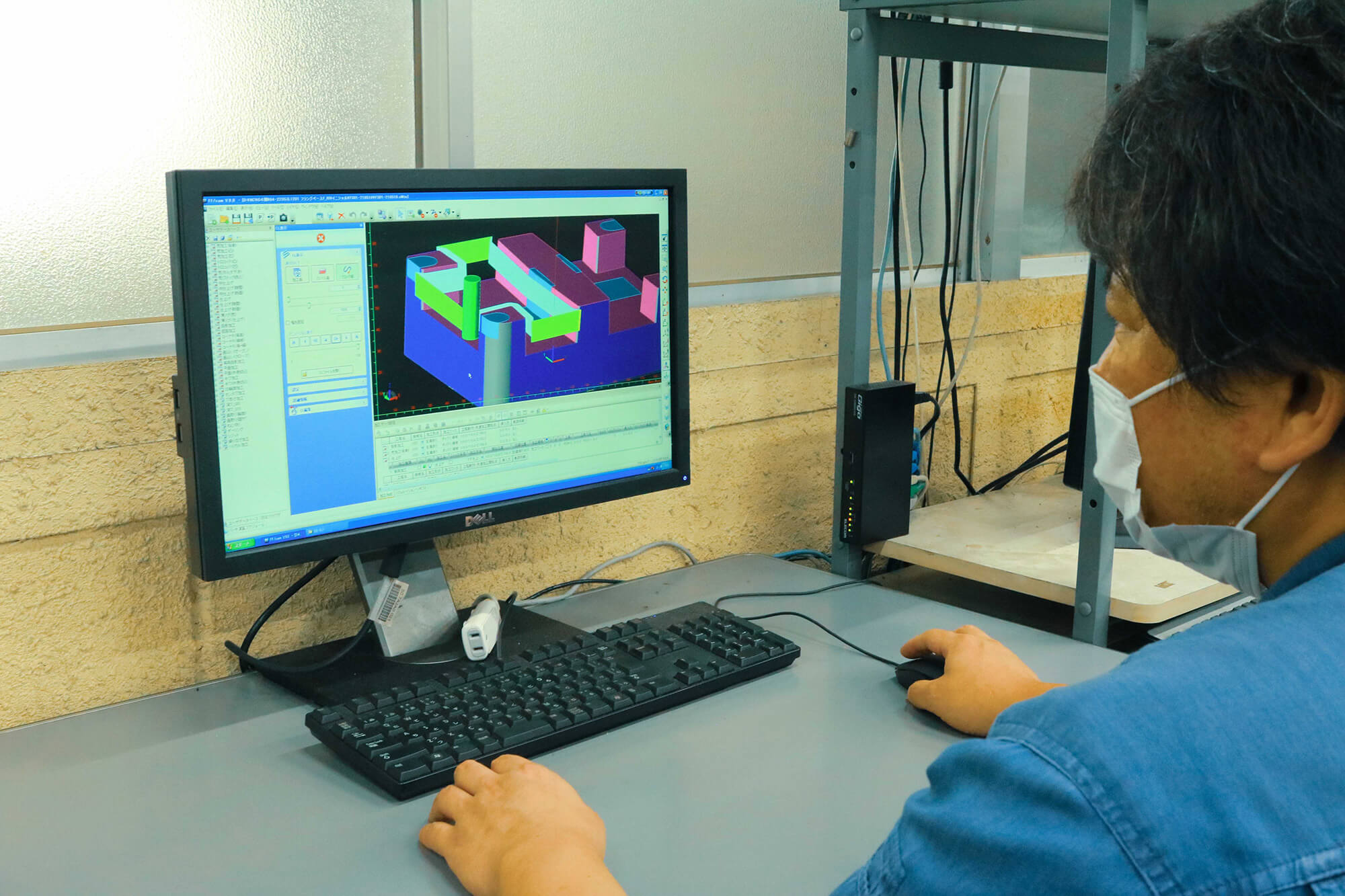
- マシニング加工
- 各種工作機を使用して金型製作を進めて行きます。
マシニングはNCプログラムによる自動運転と並行して手動で操作する工作機(切削加工、研削加工)を行います。
夜間や休日に無人運転で加工を進める事で納期短縮と残業の低減が可能となっています。
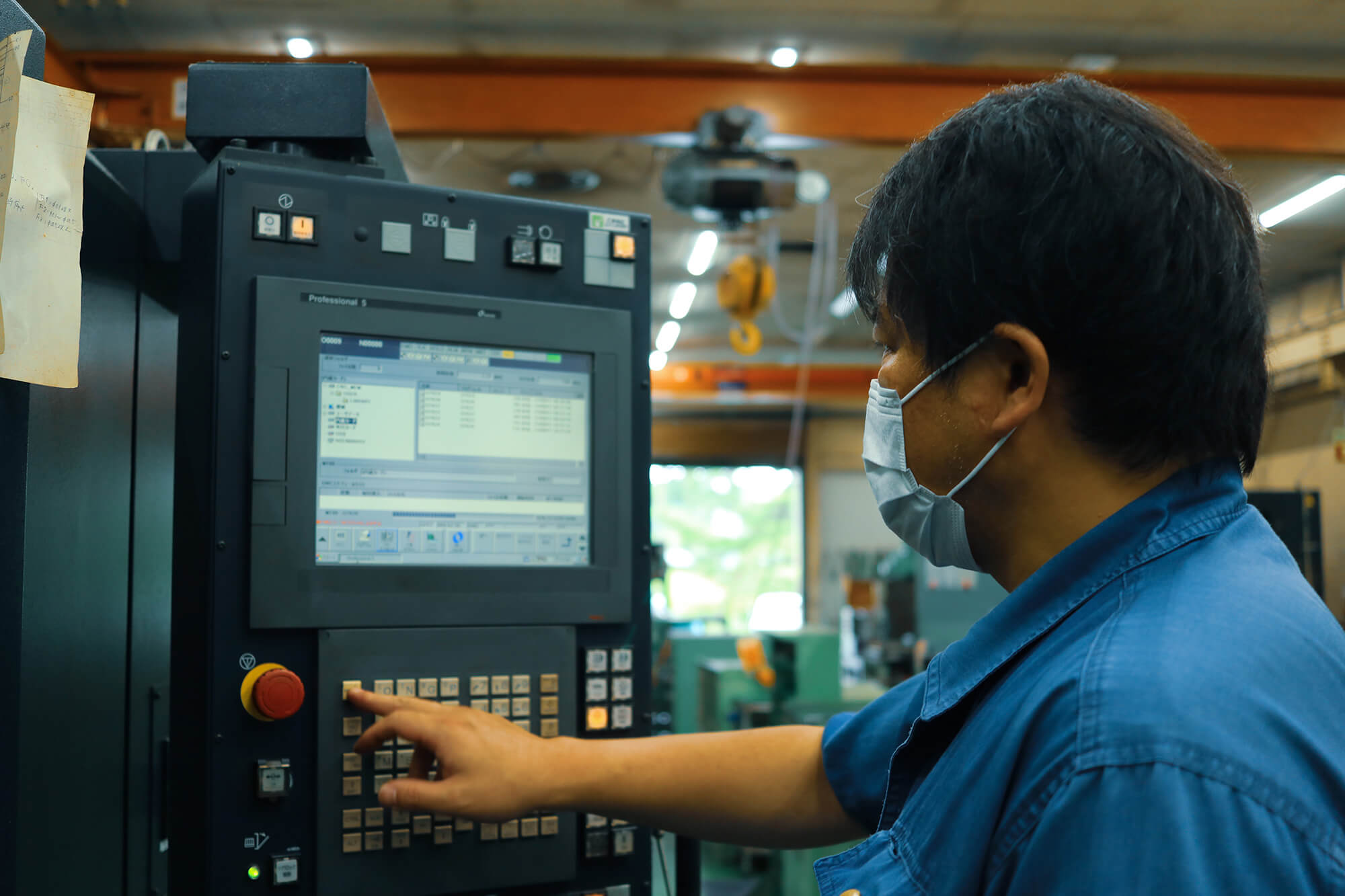
- 仕上・組込
- 図面通りに完成した各部品を金型内に組込んでいきます。
分割された入子を隙間を調整しながらベースになる型板に組込んで固定側と可動側の型合わせ部が密着し、且つ金型がスムーズに可動する様に熟練者が微調して組込んでいきます。
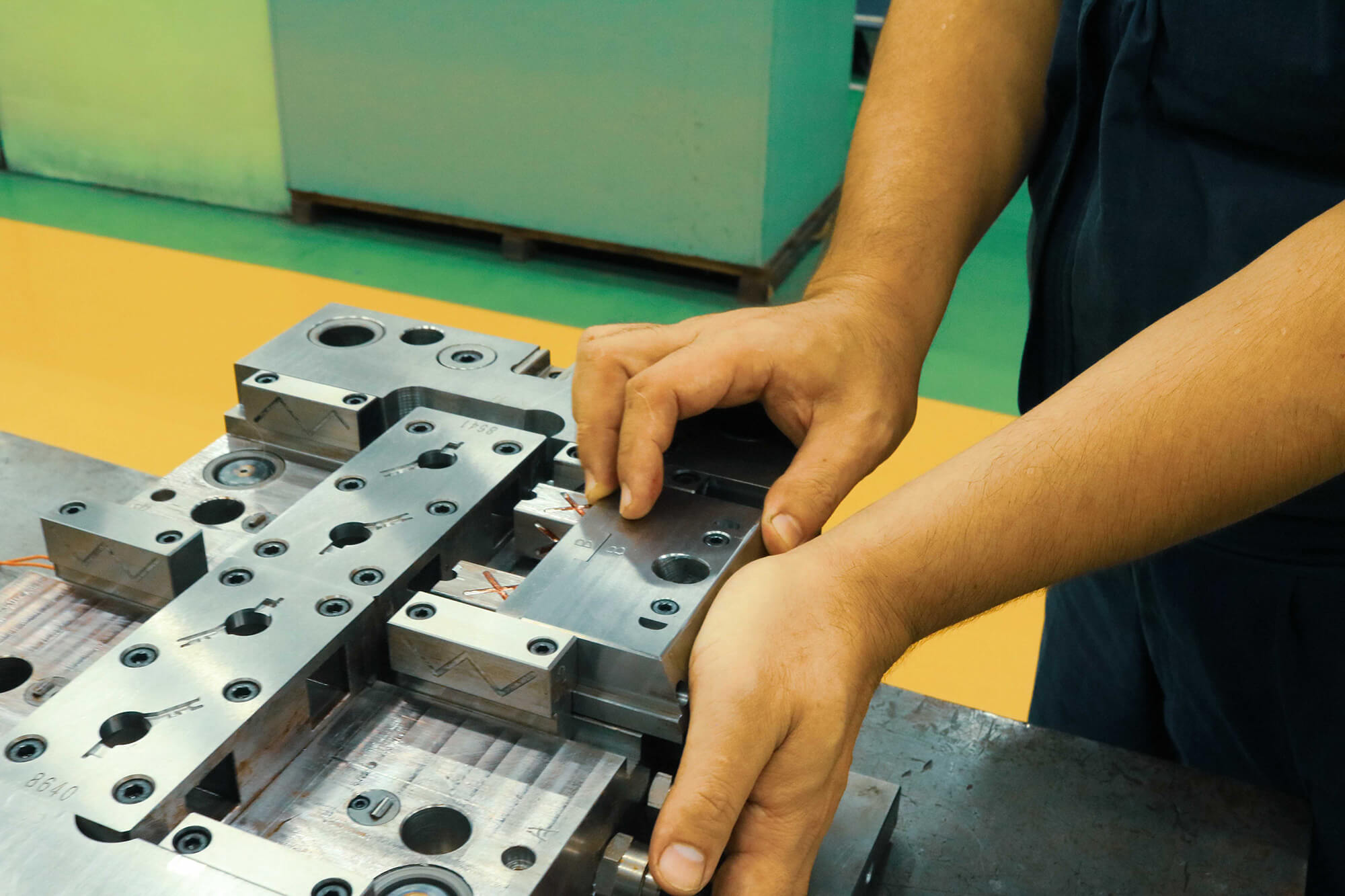
- 試作
- 完成した金型で試作成形を行い最適の成形条件を検討します。
実際に成形することで、早期に金型の問題点を見極めることができ、量産前に対応が可能になります。
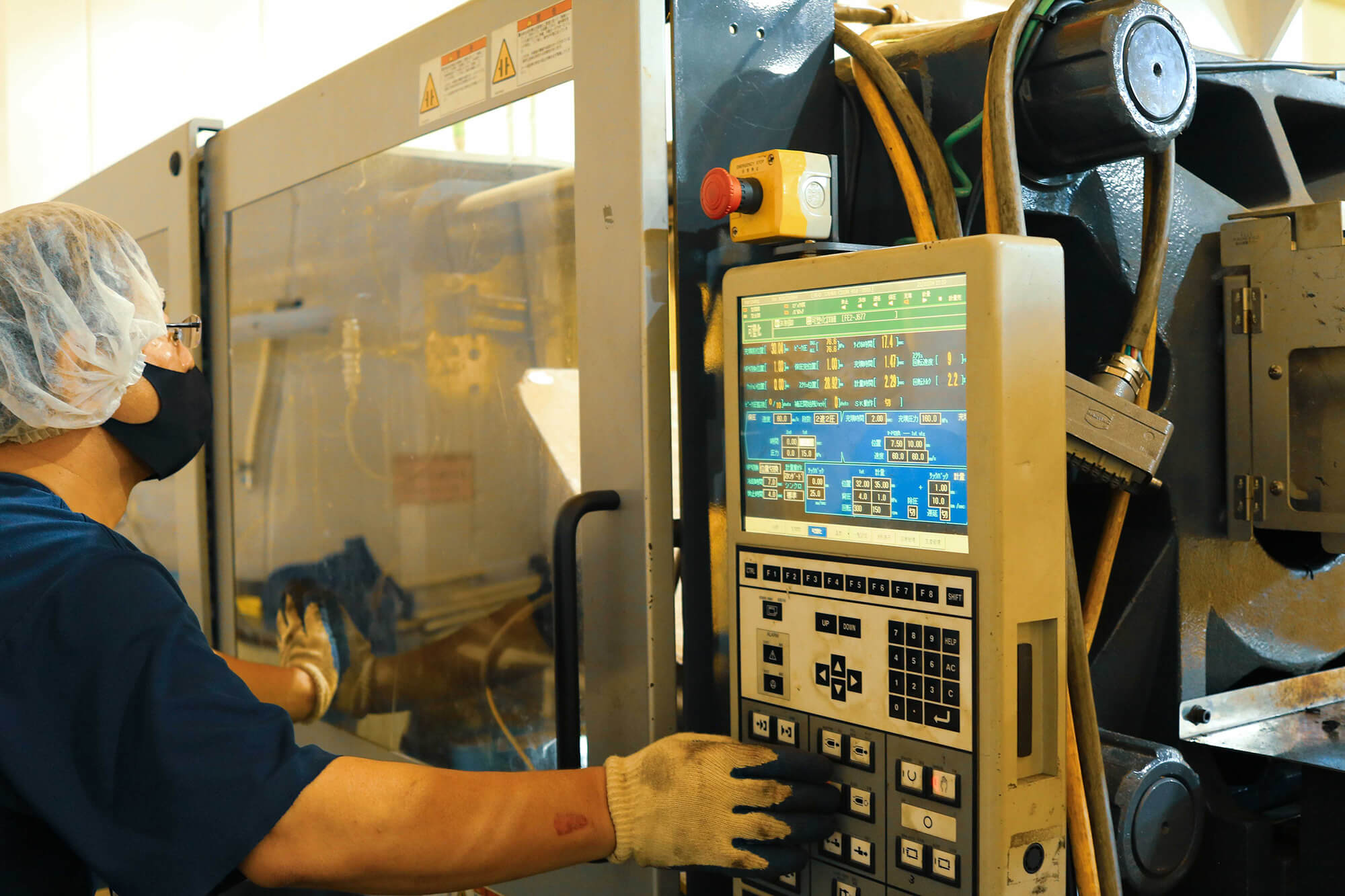
- 測定・評価
- 成形後の製品サンプルがお客様の要求している図面規格を満足しているかを検査していきます。
3次元測定機では試作前の製品が無い状態でも、事前に製品の3Dモデルを使用して測定のプランを準備し、試作後の3次元測定を効率よく行います。
製品の測定データと設計の狙い値を比較して問題がないかを確認します。設計狙い値と成形品で差が出た場合は、要因が(金型・成形・材料)を特定し対応策を検討し、再度補正を行い、加工の微調整をして完成させていきます。
- 納品
- 完成品を納品いたします。